Engineers, architects, general contractors adopt seamless system to project delivery
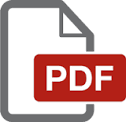
From Commercial Appeal
Related: Commercial Real Estate
General contractors, architects and engineers have been working together with owners for years to make projects better. However, the process is becoming increasingly formalized and given a new name: Integrated Project Delivery.
Integrated Project Delivery is a project delivery approach which integrates people, systems, business structures and practices through a collaborative effort.
It can be done on various levels. One level is collaboration through the early involvement of major players such as the client, architect, and general contractor seattle wa. The most intense level involves each of these parties operating under one contract from the start.
“It involves everyone coming together at the earliest stage of the project, spending a lot more time on the front end getting the right project at the right price at the right time,” Jon Summers with brg3s, formerly known as TRO Jung | Brannen Inc., says.
Flintco Inc., brg3s and Allen & Hoshall Inc. have been working together since 1986 and have collaborated on more than 20 projects.
The group is one of several vying to build a new Methodist hospital in Olive Branch. All of the teams trying for the job are using Integrated Project Delivery.
The spirit of Integrated Project Delivery has been around a long time, according to Summers, who has been working in health care for 25 years. Teams with architects, contractors and owners often work together on the front end to eliminate redundancies and problems which pop up during construction. Some companies use construction project management software to keep on top of their projects, as well as their workers to ensure that they are working together to make a project is completed with care and quality.
“The ideas of it have been around for some time, but it really started coming together around 2001,” says Steve Berger, managing principal with brg3s.
It originated on the West Coast, but the American Institute of Architects started formally defining Integrated Project Delivery around 2007.
Technological advances have really helped establish Integrated Project Delivery, according to Tim Weatherford, vice president with Flintco.
Building Information Modeling, which usually involves real-time, three-dimensional software, goes hand-in-hand with Integrated Project Delivery.
As general contractors, subcontractors, engineers and architects (like NC Architecture, for instance) have become more computer savvy over the years, everyone can participate.
“All of the members of the team work on this one computer model,” Berger says.
There are other, more traditional forms of project delivery such as design/bid/build, which is mostly used on public projects.
“Integrated Project Delivery really takes the best out of all the traditional delivery methods and tries to put a nice bow around them,” Weatherford says.
Traditionally, architects design a project and develop reams of technical drawings and documents. Contractors look at those drawings and come up with costs and schedules. They also bring in their subcontractors to get feedback on how it will be done in the field. The whole time, plans are being reviewed and altered.
“There is a whole lot of redundant effort,” Berger says.
The Integrated Project Delivery gets everyone in the same room earlier to remove some of those redundancies.
“I think that’s where some of the savings occur,” Berger says. “We’re not duplicating each other’s work. We’re working together so that everyone is in agreement on the final drawings and the way it is built in the field.”
If Rob Herd, project manager with Allen & Hoshall, had to describe Integrated Project Delivery in one word it would be “collaboration.”
“We’re bringing all these decision-makers together at one time instead of spread out across the whole project,” he says.
It speeds up the process. An example could be the architect picking a certain material for an exterior design element.
The contractor can look at it and give a price, which could affect whether it makes it in the final design or not and whether it fits in the budget. A masonry subcontractor can offer alternative materials or details quickly instead of a week later.
Changes to a project can affect how much money in the budget is available for other parts of the project. With everyone there, a change recommended by a subcontractor can be made by the architect, all with the owner’s approval and input.
“All three parties are responsible for all assets of the budget,” Summers says. “No one making a decision is isolated from anyone else.”
Flintco Inc. General contractors HQ: Tulsa, Okla. Division president: Kevin Moyes Local employees: 776 Local address: 2179 Hillshire Circle Local phone: (901) 372-9600 Website: www.flintco.com aashby@bizjournals.com | (901) 259-1732